Was sind die häufigsten Lagerschäden?
- 2020/8/6 14:35:50
Lager sind ein unverzichtbarer Bestandteil mechanischer Geräte. Um den Reibungskoeffizienten zu verringern und mechanische rotierende Körper zu tragen, müssen wir häufig Lager verwenden. Beim täglichen Gebrauch mechanischer Geräte verursachen Umweltfaktoren und menschliche Betriebsfaktoren jedoch häufig bestimmte Schäden an den Lagern. Zu diesem Zeitpunkt müssen wir die Lager austauschen oder den Hersteller für Reparaturen suchen. Dies führt zweifellos zu einem gewissen Druck auf die Nutzungskosten. Das Verständnis des Mechanismus der Lagerbeschädigung und die Klärung der Faktoren, die die Qualität des Lagers beeinflussen, helfen uns daher, das Lager besser zu nutzen.
1. Lagerverschleiß
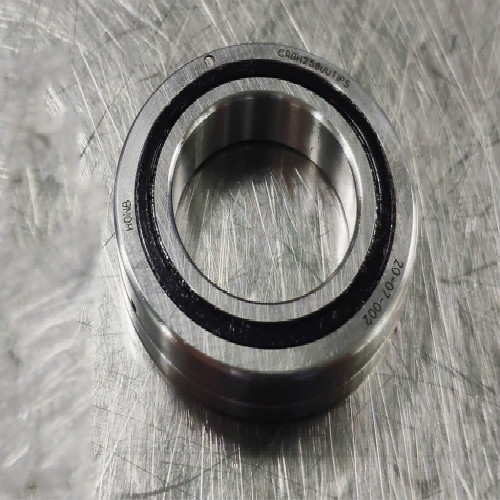
1. Schleifschäden: Wenn winzige Fremdkörper in das Lager gelangen, kann dies zu übermäßigen Schleifschäden am Lager führen. Beispielsweise verschleißen oder schleifen Sandpartikel, Metallpartikel, die beim Schleifen und Bearbeiten entstehen, und Metallpartikel oder Karbide, die durch Zahnräder gebracht werden, Walzen und Laufbahnen. Dieser Verschleiß kann dazu führen, dass sich das Axialspiel oder das Innenspiel ausdehnt, wodurch die Lebensdauer des Lagers verringert und die Exzentrizität des Lagers verursacht wird.
2. Markierungen und Kratzer: Harte Partikel, die im Lager rollen, können Lochfraß und Kratzer auf den Rollen und Laufbahnen verursachen. Metallteile oder große Staubpartikel, die durch unsachgemäße Reinigung des Lagersitzes zurückbleiben, verursachen vorzeitige Ermüdungsschäden.
3. Rillen: Rillen sind extrem starker Verschleiß, der durch Schmutz oder Metallpartikel verursacht wird. Diese Verunreinigungen werden in das weiche Käfigmaterial eingeklemmt, was zu Kerben in den Wälzkörpern führt, die die Wälzkontaktgeometrie beeinflussen und die Lebensdauer des Lagers verringern.
4. Verschmutzung durch Schmutz: Die Verschmutzung durch Fremdkörper wird normalerweise durch Staub, Sand und Umweltpartikel verursacht, während die Verschmutzung durch inneren Schmutz im Allgemeinen durch unsachgemäße Reinigung von Zahnrädern, Keilen, Dichtungen, Kupplungen, Bremsen, Gelenken und Lagersitzen verursacht wird. Oder Teile sind beschädigt oder abgezogen. Während des Schmiervorgangs wandern harte Partikel im Lager und verursachen schließlich Kratzer (Quetschungen) an der Innenfläche des Lagers. Die Vertiefung bildet Vorsprünge, die die Konzentration der Oberflächenspannung verursachen, die Lageroberfläche frühzeitig beschädigen und die Lebensdauer des Lagers verkürzen.
2. Lagererosion
Erosion oder Korrosion ist eines der schwerwiegendsten Probleme bei Wälzlagern. Die hochpräzise Bearbeitung der Lagerlaufbahn und der Rollenoberfläche macht sie extrem anfällig für Korrosion durch Feuchtigkeit und Wasser.
Erosion wird normalerweise durch Temperaturänderungen im Lagergehäuse, interne Luftkondensation und kontinuierliche Ansammlung von Feuchtigkeit verursacht. Feuchtigkeit oder Wasser gelangen häufig durch beschädigte, gebrochene oder unsachgemäße Dichtringe in das Lager. Darüber hinaus kann eine unsachgemäße Reinigung und Trocknung des Lagers während der Demontage und Inspektion solche Schäden verursachen. Nachdem das Lager gereinigt und getrocknet wurde oder wenn das Lager ins Lager gebracht wurde, sollte es mit Schmieröl oder anderen Konservierungsmitteln beschichtet und mit Schutzpapier verpackt werden. Unabhängig davon, ob es sich um ein neues oder ein altes Lager handelt, sollte es an einem trockenen Ort platziert und in die Originalverpackung eingewickelt werden, um die Möglichkeit statischer Korrosion vor dem Einbau zu verringern.
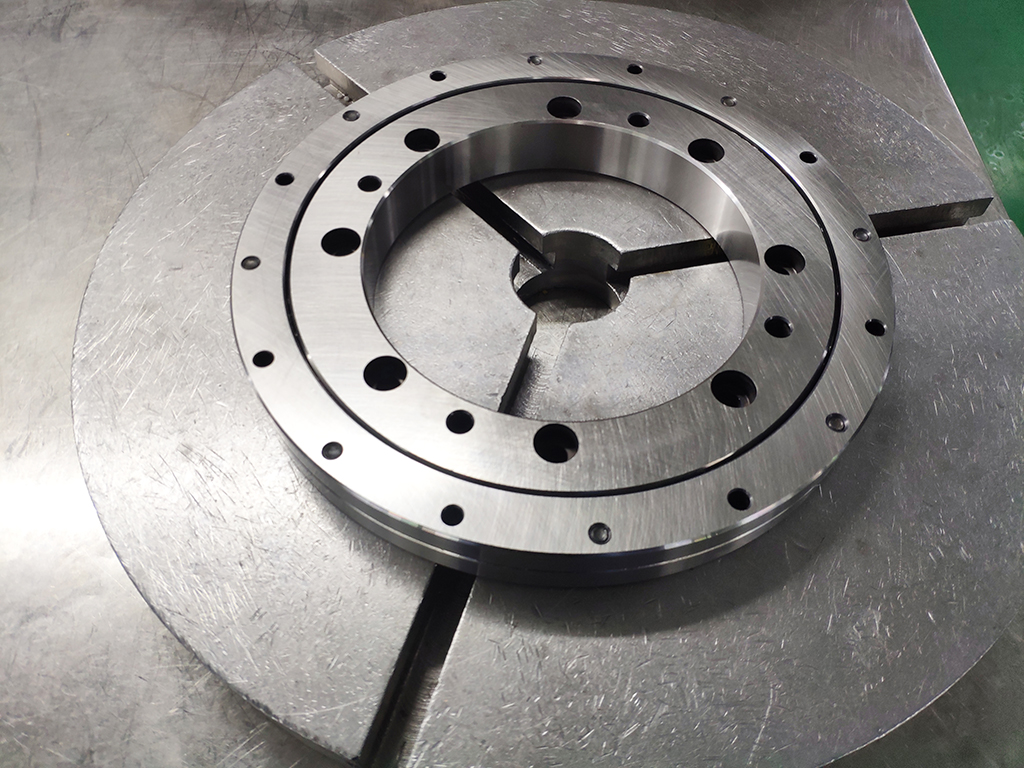
Lagerschäden durch unzureichende Schmierung können sich unterschiedlich verhalten. Es kann sich um eine sehr leichte thermische Verfärbung handeln, die mit einem Abrieb des großen Rollenendes einhergeht, oder es kann sein, dass das gesamte Lager mit extremer Metallverformung blockiert ist. Es gibt auch eine solche Situation: Das Lager erfährt einen Trockenstart, begleitet von extremen Metallverzerrungen, aber seine Oberfläche bleibt immer noch hell; Dieses Phänomen tritt gelegentlich auf. Dies liegt daran, dass während der Anlaufphase das Lager durch Metall-Metall-Kontakt thermisch beschädigt wird und das Lager schließlich abkühlt, sobald das Schmiermittel das Lager erreicht. Dann versuchte das Lager, sich selbst zu „reparieren“, um die anfängliche Metallverformung und thermische Verfärbung zu verbergen.
Sekundärschäden sind offensichtlicher und maskieren häufig das anfängliche Problem und die nachfolgenden Lagerschäden. Die typische Leistung dieser Art von Lagerschaden besteht darin, lokal hohe Hitze und Metallströmung im Lager zu verursachen, wodurch die ursprüngliche Lagergeometrie und das Lagermaterial geändert werden. Sichtbare Metallrisse, Kratzer, Hitzeflecken, Verformungen oder geometrische Veränderungen machen das Lager zu einem Abfallprodukt und sind daher nicht mehr verwendbar.
4. Lagerüberlastung
Übermäßige Vorspannung erzeugt viel Wärme und führt zu Lagerschäden. Das Schadensmuster ähnelt dem, das durch unzureichende Schmierung verursacht wird. Diese beiden Ursachen werden häufig verwechselt, sodass eine gründliche Prüfung erforderlich ist, um die Ursache des Problems zu ermitteln. Für den allgemeinen Betrieb geeignete Schmiermittel sind möglicherweise nicht für Lager mit hoher Vorspannung geeignet, da die Festigkeit des Ölfilms möglicherweise nicht stark genug ist, um extrem hohe Lasten aufzunehmen.
Selbst wenn ein Hochdruckschmiermittel verwendet wird, das schwere Lasten tragen kann, kann unter hoher Vorspannung eine andere Form der Beschädigung auftreten. Obwohl das Schmiermittel die Last bewältigen kann und verhindert, dass das Wälzkörper oder die Laufbahn zerkratzt wird, kann die schwere Last ein vorzeitiges Ablösen der Untergrundschicht durch Ermüdung verursachen. Das Auftreten dieser Art von Abplatzungen und nachfolgenden Problemen mit der Lagerlebensdauer hängt von der Vorspannung und der Tragfähigkeit des Lagers ab.
5. Lagerbetrieb und Einbau
Bei der Handhabung und Montage des Lagers ist Vorsicht geboten, und die Wälzkörper, Laufflächen und Kanten dürfen nicht beschädigt werden. Wenn sich auf der Laufbahnoberfläche eine tiefe Rille befindet oder wenn die Wälzkörper getroffen oder verformt werden, wird das Metall in der Nähe des beschädigten Bereichs entsprechend angehoben. Wenn die Wälzkörper diese beschädigten Oberflächen passieren, werden hohe Spannungen erzeugt und verursachen lokales vorzeitiges Abplatzen. Die direkte Auswirkung von Rillen und tiefen Markierungen besteht darin, das Lager rau zu machen und Vibrationen und Geräusche zu verursachen.